4
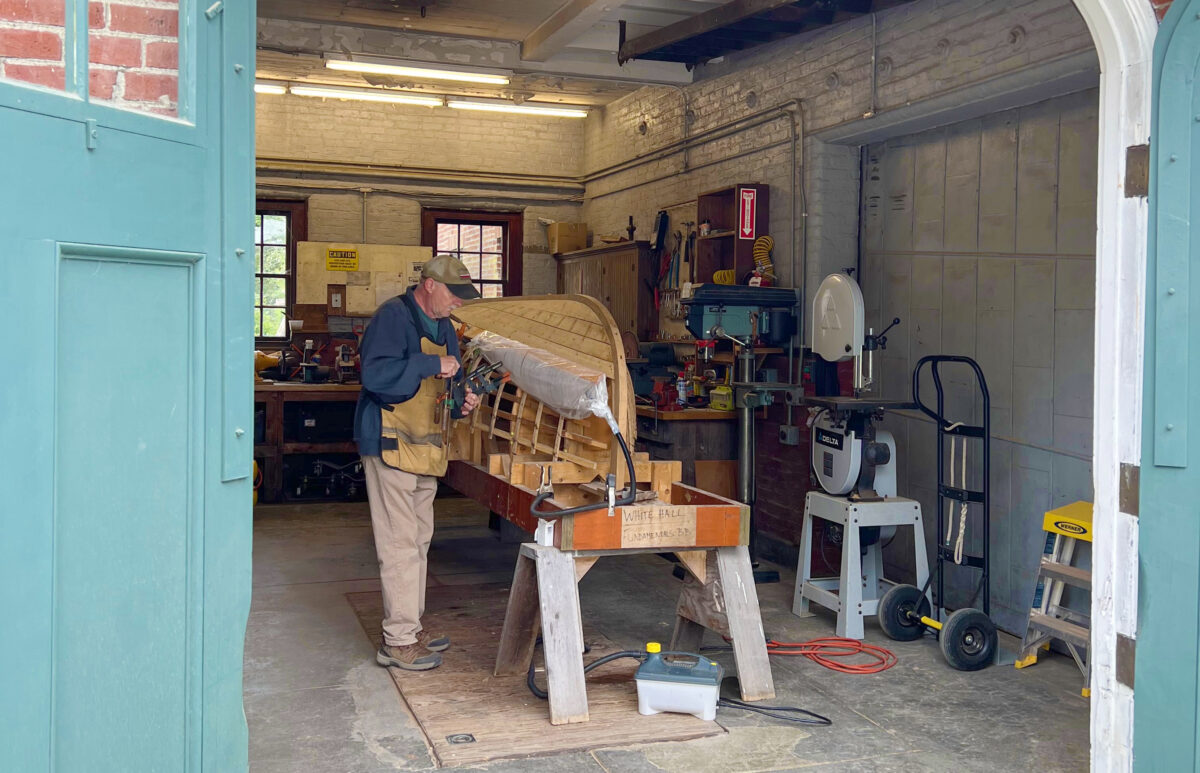
October 2024
Boil-in-the-Bag Plank Bending
Using a portable steambox to steam planks
Sponsored By WoodenBoat School
4
October 2024
Using a portable steambox to steam planks
7
September 2024
How to mark your anchor rode for water depth and scope
3
August 2024
4
July 2024
Modifying a trailer for dry-feet launching
15
June 2024
A home-built go-anywhere cart
7
May 2024
Bringing unique flair to plywood and strip-built kayaks
6
April 2024
Dying synthetic rope for a natural look
14
Small Boats Annual 2015
A guide to common construction methods
14
March 2024
An alternative approach to securing floorboards
11
February 2024
Making filters more effective and longer lasting
25
January 2024
Keeping the heat in camp-cooked meals
22
December 2023
A simple sewing project for comfort in camp
27
November 2023
Better than bungees, cheaper than straps
15
October 2023
Two techniques for tangle-free tosses
8
September 2023
Keeping trailer lights out of the water and in the line of sight
6
August 2023
Oilite bearings to reduce wear
6
July 2023
The powerful pull of neodymium
Small Boats Annual 2014
Four more small boat tents
Small Boats Annual 2014
Boatbuilding never ends with launching day
5
June 2023
Using duct tape to make sandpaper more durable
20
May 2023
Made with ordinary rope and knots
6
April 2023
Lifting a boat with a winch and a cordless drill
Small Boats Annual 2012
Small Boats Annual 2012
Small Boats Annual 2012
Part of common sense is good preparation