People need to see where they are going; racing-shell rowers and hockey’s defensive players are about the only ones that don’t. For the rest of us rowers, there are times and places where being able to see the path ahead is really certainly useful.Rowing in tightly constrained water or in the midst of boat traffic is challenging unless there is a cox steering the boat. So, rowers in Venice’s narrow canals and in Louisiana’s winding creeks and bayous stand and row facing forward, while lobstermen in Maine who work around rocks and ledges and in narrow coves and inlets set up their peapods or double-enders to be rowed facing forward.
Join The Conversation
We welcome your comments about this article. If you’d like to include a photo or a video with your comment, please email the file or link.
Comments (10)
Leave a Reply
Stay On Course
With some help from Ben via the WoodenBoat forum, I put together a pair of oarlock extensions for my row-cruising Walkabout (just noticed that was 7 years ago now!). The ones I made are 1/2″ stainless steel rod with an Oilite bushing, held together with canvas phenolic tubing. I did some trials with adjustable rods, and found 13″ of extension was most comfortable. These are used in the forward (out of 3) rowing positions on my boat, putting my standing weight near center. Support blocks below the oarlocks were needed to take up the increased torque of the long lever, as you note in the article. The 8″ extensions on the oar handles put my hands in the most comfortable and best power position.
Power is less than slide-seat rowing, but standing works well for maneuvering to a dock, puttering along a shore while birdwatching, and just taking a break from sitting.
A photo set of my project is on Flikr.
I’ve made two pair of extensions with heavy-walled naval-brass tube and 1/2″ brass rod. They’re quick and easy to make and they are extremely strong. I haven’t had a failure, but I suspect the oarlock socket is the weak spot.
David,
All of the old working pod rigs have a “step” of some kind below the oarlock socket. I’ve also looked at rigs on hunting boats where they need extensions for pulling. Here again there is a block of some kind to take the bottom of the extension. In the case of the old pipe extensions on the hunting boats, they just got through a plate with an appropriate hole drilled in it, then to a block.
You might find the attached photo montage interesting. The montage depicts DIY oarlock extensions installed on my Drascombe Lugger (Lugger 801). The photos were taken this past summer (2021) during my sail/row/motor downstream the Lower Snake and Lower Columbia (27 boat days, Lewiston, Idaho to Astoria, Oregon). In the montage I’m departing the marina at Cascade Locks, Oregon, just upriver of Bonneville Dam. Throughout the journey the standup/forward facing row position was of particular value each evening (and the following morn) when searching-out a nearshore anchorage (preferable tucked tight into the weeds, out of wind and current, see photo attached of Lugger 801 anchored near Beacon Rock, which is in the photo background).
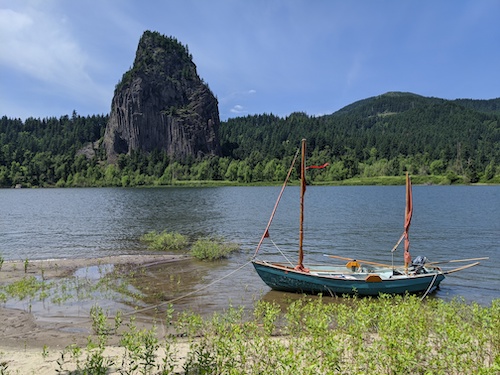

It appears that the extensions put oarlocks at about waist level while sanding. Am I correct?
Extention at waist level while standing?
Eric – I found putting oar handles at chest height works best. Most of the stroke is just leaning body weight onto the handles, with a straight arm push at the end. Chris’s photo on his garvey looks the same.
I am building an Acorn 12 and will keep all of this stuff in mind as I go. It will also be much easier to read the water depth when standing up.
When sailing in the lagoon of Grado (Northern Adiatic, Italy) with my Harrier, I took some pictures of an old wooden fishing-boat, a Batela, which is always rowed standing up and facing forward.
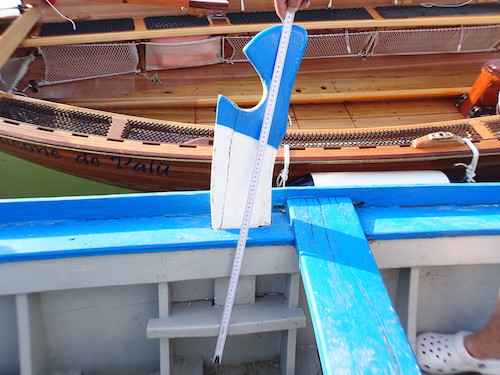
Batelas have a flat bottom, the wooden tholes are called forcole.
Waist level would be low for efficient pushing. As noted above, chest would be better. There are three variables: boat beam, oarlock height and oar length. Not obvious until you draw it for a given boat beam and height, longer oar length if you just get the blades in means a lower push angle. It looks like the Maine fishermen just used their pulling oars for pushing.
My friend Joe Auciello just set up some push locks in his Skerry, using iron pipe for extensions. He experimented on his trailer. Got in the boat, started with high extensions maybe a foot, used his regular oars, and trimmed the extensions down to what worked: a chest push, blades below the waterline. We discussed hand spacing, and figured that pushup spacing would be about right. He also looked at where he needed to stand and was able to site his oarlocks accordingly. The regular sockets were too far aft. Only after he had things to his liking did he make a block to take the foot of the oarlock.