We have spent some time with plywood boats over the last several years, both vintage and new, and a common problem that we have had to address is cracks that can develop in the outer veneer of the plywood. When plywood is made, the wood fibers are stressed from their original shape to form flat veneers, and over time the wood dries out and the fibers shrink. Repeated wet-dry cycles and sun exposure also can cause damage to veneer protected only by paint or varnish. The cracks, also referred to as checking, can be very fine or larger fractures that form a rough surface. At worst, there can be voids where bits of veneer have chipped off.

The fir plywood deck was showing every bit of its age, some 70 years. The area in front of the sander has been partially sanded, removing the high spots created by the checking of the top veneer.
Applications of epoxy, both straight and thickened with silica, have been very effective in repairing the plywood and preventing further checking. Epoxy has adhesive and sealing properties that are superior to those of paint. Applied to bare wood, epoxy stabilizes the grain and provides a protective barrier to water intrusion. It provides a solid base for subsequent applications of varnish or primer and paint. If the surface being restored is especially rough, as it can be with fir plywood, fairing compound can make it smooth.
We built our Penobscot skiff with okoume plywood five years ago. The instructions provided by designer Arch Davis prescribed two coats of epoxy to seal the grain of the veneer before applying fairing compound to smooth the irregularities caused by the plywood and fastener holes; primer and polyurethane paint on the hull; and alkyd primer and paint for the topsides. The plywood has not checked and the finish is still smooth.
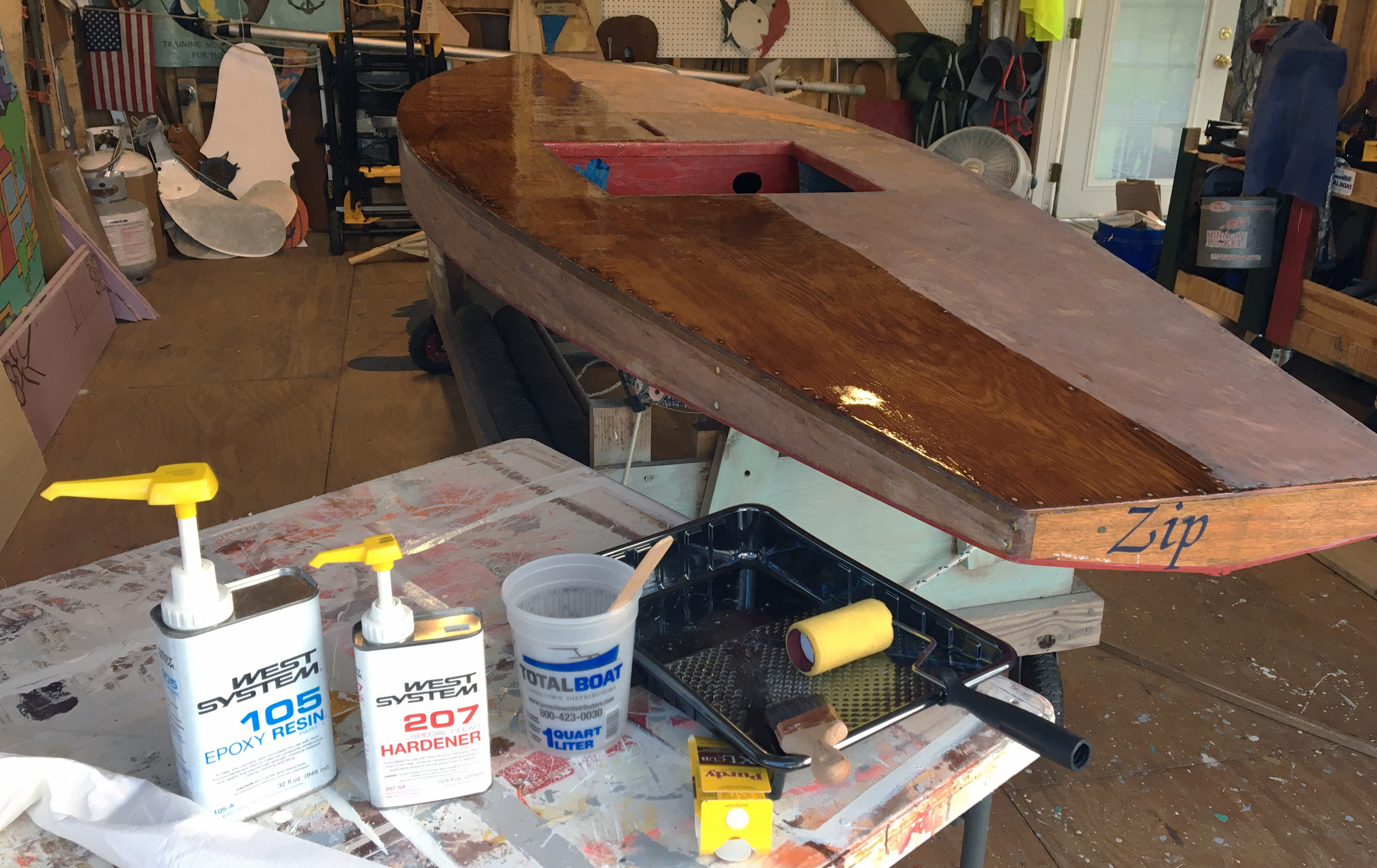
A foam roller is used to apply the first coat of epoxy, sealing the wood grain and filling the voids created by the checks in the plywood. Subsequent coats of epoxy, applied after sanding, will level the surface. Here WEST System’s 105 epoxy resin is being mixed with the 207 special clear hardener as a way to achieve a bright finish.
Arch’s advice got us thinking about using epoxy on a 1953 Alcort Sunfish. The painted fir plywood deck had extensive checking. We sanded it back to bare wood and applied two coats of WEST System 105 Resin with 207 Special Clear Hardener, which sealed the grain and gave the deck a nice bright finish. That deck has not checked since 2013. We store the boat in our garage when not in use, so there was no need to varnish over the epoxy to protect it from the sun’s UV rays.
We also used epoxy to treat two plywood Alcort Sailfish. The Standard Sailfish had the original 1950s deck and hull panels, which we sanded to bare wood; the Super Sailfish got new plywood for the bottom. It was easy to roll two coats of epoxy on the new plywood as well as on the sanded original panels, sanding between coats. Both Sailfish were to be painted, so we could apply an epoxy-based fairing compound and sand the surface smooth before priming and painting. There has been no checking on the old or new plywood since 2016 and 2019, respectively. The Standard Sailfish was painted with alkyd enamel, and the Super Sailfish was painted with a one-part polyurethane. A wide variety of paints can be used as long as they are applied over a good epoxy-compatible primer.
For small cracks and larger voids—bits of veneer that have come loose—we have used TotalBoat’s THIXO (epoxy thickened with silica) to fill the voids and provide a smooth surface for fairing compound, primer, and paint. The THIXO can be applied over sanded, clean surfaces, so it was not necessary for us to remove well-adhered paint to get to bare wood. We have not had checking through the silica-thickened epoxy either; it is stronger than straight epoxy.
Application of epoxy is just as easy as painting and restores checked plywood to like-new condition. It is not necessary to apply fiberglass cloth unless cloth is desired for specific high-wear areas. And, if you’re building a new boat, coating the plywood with epoxy before painting or varnishing is a step well worth the time and expense.
When not treating checked plywood, Audrey and Kent Lewis mess about in their armada of 16 small boats. Their adventures are logged at www.smallboatrestoration.blogspot.com
For the editor’s perspective on checking and his repairs inspired by this article, see “Checking My Work” in this issue.
You can share your tips and tricks of the trade with other Small Boats Magazine readers by sending us an email.
In my experience, Doug fir plywood is the worst of all. Because of this, I would never again build a small boat using the stuff. I have ‘glassed plywood hulls, but again, would not bother to do this with polyester resins, as I have seen delamination occur. I hypothesize that this happens because fir plywood (which has alternating hard and soft grain) doesn’t soak up polyester very well in those places where the grain is hard.
I know people who like vinyl ester, but I have no experience with it myself.
One advantage of epoxy is that it loves to seek the lowest point, and will run into crevices and fill them, especially if forced into the grain with a roller under pressure. I sometimes compare this tendency of epoxy to the behavior of honey on a piece of toast with holes in it.
A nice photo of restored plywood Sunfish ZIP, under sail, appears in on-line Antique Classic Boat Society, Sept. 17, 2015. Great piece of work.
I have built many small, simple boats with fir plywod. It’s strong, rot resistant, lighter than pine plywood and readily available from building supply stores. But it checks, oh Lordy, how it checks! I’ve used sealants, primers, epoxy resin, oil and latex paints. The boats have been stored mostly outside, under a tarp on a frame in shade. I live in a temperate zone (East coast, Chesapeake Bay). Here’s what I experienced:
Sealers, primers, fillers, paints don’t stop checking.
Epoxy coating slightly delayed checking, but never stopped it. Epoxy filling a checked piece only reset the clock for a couple seasons. And it was expensive in labor and material.
The only thing that worked was to glue a covering to the exposed surface. I’ve used fiberglass, Dynel, and unbleached cotton canvas. All worked great, no checking, ever.
An alternative is MDO (medium density overlay, or “signboard”) a fir ply with a heavy paper/resin veneer that never checks and glues and finishes beautifully. It has few/no voids. It comes 3/8” and up, coated on one or both sides. You won’t find it at BigBox stores, but other suppliers stock it or will order it for you. Prices are about halfway between plain fir and okoume (2021 prices). Pine plywood checks badly, too.